
Atlas Manufacturing greenhouse sales rep Stuart Sumner says interest in new structures has never been higher. “We have customers in various sectors of this industry that had very productive years despite COVID-19,” he says. “Due to this, we are seeing more interest and enthusiasm in 2021.”
According to Sumner, the following five trends in greenhouse structure innovation seem to be popping up more and more across the projects he has worked on over the past year:
Positive pressure (PP) ventilation cooling — Greenhouse growers are taking a closer look at PP ventilation systems, especially in hot and humid climates where a traditional system that draws more humidity from outside is not ideal, Sumner says. “When growing in a high humidity climate, adding additional humidity through an evaporative cooling system in a negative pressure setting can have a detrimental effect on crops,” he says. “You will be much more likely to experience issues with fungal pathogens and have a greater need for humidity control equipment.”
Supplemental lighting — Sumner answers a lot of questions about supplemental lighting during the design phase. “There is a lot more interest surrounding LED options for supplemental lighting and the technology itself is rapidly evolving,” Sumner says. “Companies are constantly innovating these lights to be more energy efficient and effective at targeting the desired spectral wavelengths of PAR light. The traditional HPS fixtures may be the most commonly used at this time, but I believe the LEDs may overtake them as the most frequently used at some point in the future.”
Taking sidewall height even higher — Growers are also interested in installing the highest sidewalls structurally possible in new builds, Sumner says. This strategy allows for a larger area at the top of the structure to push and store hot, humid air far away from the plant canopy down below. In the past, growers were wary of going too high on sidewall design due to having to heat or cool that larger volume of air. That is a commonly held misconception that is changing as growers learn more about how the structure itself, HVAC systems, climate controllers and ventilation all interface together, according to Summer. “It’s true that the higher you can go [on sidewalls], the more optimal situation you are in from a ventilation and cooling perspective,” Sumner says. “With everyone wanting to get those sidewalls as high as they can be, I like to joke that by 2050 we’ll all be growing crops in skyscrapers.”
Hydroponic grow systems — From the ubiquitous “Dutch” bucket style for peppers and tomatoes to the popular vertical farming and deep-water culture growing systems, grower interest in replacing soil with growing media and oxygenated water has never been higher. “We are seeing commercial growers utilizing hydroponic grow systems such as Nutrient Film Technique (NFT) systems that can reduce the expected harvest time considerably when compared to more traditional grow methods.”
Insect exclusion structures — Companies like Atlas are recommending growers, regardless of crop, consider built-in insect protection measures. Sumner refers to these design add-ons as “insect exclusion structures.” Extending the frame of the greenhouse out on opposite ends a set distance, and then covering that area between the ventilation equipment and the outside with woven, insect-proof materials helps prevent insect intrusions. “This is something that we really think is worth a grower’s investment in the long term. It will save you money,” he says.
Q&A
NGMA member-company GrowSpan (South Windsor, Connecticut) agreed to answer some of our questions regarding developments of late in the greenhouse structures segment.
Greenhouse specialist Adrian Valois spoke with us on behalf of the greenhouse manufacturer.
Greenhouse Management: What are some common requests that you are seeing more of when it comes to greenhouse expansion projects?
Adrian Valois: Every project that we work on is different, we have projects all over the country and different growers have different needs based on location and crop. When people are planning for expansion, we recommend getting an irrigation system that is easy to expand upon, and a controller that can handle future greenhouses for automation. Corridors are another popular request when looking to expand. These can either be an extension of the greenhouse using polycarbonate, metal cladding, or insect netting.
GM: When it comes to expanding production, are you seeing more growers that want to build new? Or are growers more focused on how they can get more out of the structure they already have – by doing things such as raising production lines to a second or even third level?
AV: In greenhouses, we do not typically see multi-level systems as it defeats the purpose of having a greenhouse that can take advantage of sun light as their main source of light. Adding layers means that there will be a higher need to add artificial lighting in your greenhouse. Therefore, when people want to increase production, they build more greenhouses. Gutter connected greenhouses make this extremely easy as they can be easily added to an existing structure (like our S1000 and S2000 commercial models).
GM: How has the supply chain issues with building materials affected the greenhouse construction business?
AV: Supply chain has been a struggle for many businesses, including greenhouse manufacturing. Shortages of steel and polycarbonate have affected all greenhouse manufacturers, but we made sure to have enough of these in our warehouses to keep up with demand. We are hoping to go back to normal by 2022, but nothing is certain.
GM: Labor has also taken a huge hit during the pandemic. Are more growers looking for automation technologies integrated into the greenhouse?
AV: Automation is a huge part of the greenhouse industry nowadays. This is mostly true when it comes to automating the environment, but it is hard for new growers to automate their growing systems as the capital expense is too high. This is something people start investing into once they have multi-acre facilities.
GM: Anything else to share with our audience of growers?
AV: Always consult with a greenhouse specialist when trying to modify your greenhouse. I have traveled to some greenhouses where they decided to make some modifications that made expansions extremely complicated, and they lost a lot of money in the process. Such as, evaporative coolers that needed to be moved, exhaust fans that needed to be replaced with proper sized ones, automated shade systems that needed to be fixed, and more.
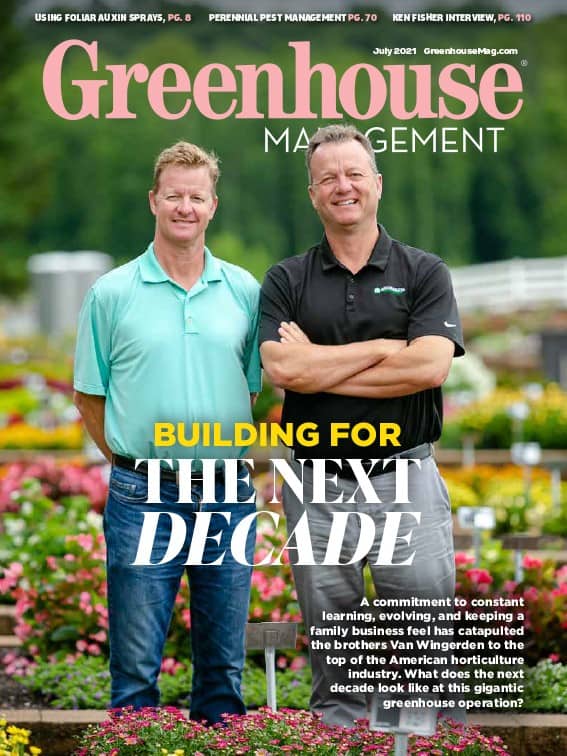
Explore the July 2021 Issue
Check out more from this issue and find your next story to read.
Latest from Greenhouse Management
- Chilli thrips (Scirtothrips dorsalis)
- GS1 US Celebrates 50-Year Barcode 'Scanniversary' and Heralds Next-Generation Barcode to Support Modern Commerce
- University of Florida offers Greenhouse Training Online program on irrigation water
- Flower trends in full bloom
- ‘Part of our story’
- Dramm introduces new hose, sprinkler attachments for home gardeners, nurseries
- Nominate an outstanding leader
- Profile Products hires sales and business development manager for Europe and Asia