

Fuel prices are rising rapidly again. As of July 15th, when I wrote this column, wholesale natural gas and fuel oil have risen about 50% and propane about 70% since the first of the year. Part of this is due to inflation and part of it is related to supply and market conditions. Looking back at the charts, it seems that this peaking occurs about every three to four years.
As heating costs are the second-highest production item after labor for many growers, it is important to spend some effort to keep these under control. In past columns, I have reviewed many of the common conservation measures that growers can take to reduce energy costs.
The most common measures of insulation, heating system servicing, air circulation, controls and infiltration were reviewed in the October 2018 column (bit.ly/energy-costs-inflation). Here are three additional measures that you may want to consider:
Purchase fuel now – By purchasing the fuel early in the heating season, you can take advantage of lower prices, as charts show that the price usually increases as we get into the colder weather. Filling tanks at a low price now may save considerable money. Some growers that use propane or fuel oil have added additional tank capacity both for acquiring a lower bulk price and to have additional reserve capacity for the winter.

Preheat the fuel – Above-ground tanks and piping are subject to harsh cold weather that reduces flow. In propane, volatilization and pressure decrease with lower temperature. Propane volume decreases and becomes more dense as the temperature falls. An alternative is to install a buried tank that will keep the gas at ground temperature. Electric tank heaters are also available from Power Blanket. Some growers have ducted heat to a tank shelter through the wall of the greenhouse. In cold weather, keep the tank at least 1/3 full. Fuel oil can become sluggish and cause the paraffin to congeal. Warm oil will improve atomization and increase efficiency due to smaller droplet size. A plastic shelter over the tank can provide some additional heat and wind/snow protection. Adding methanol to the oil will reduce the viscosity. An alternative is to move the tank inside the greenhouse. Although it may take up growing space, it will keep the oil at room temperature. Exterior supply lines should be insulated with a waterproof pipe insulation.
Replacing and upgrading the energy screen material – Many of the materials that have been installed have an 8- to-10-year useful life. From inspection, I have found that the screen material becomes worn and starts to split. The aluminum foil on the polyester strips starts flaking off. The edge seal material deteriorates and can leak considerable heat to above the screen. Old screens can lose about 25% of the heat as compared to a replacement material.
L.S. Svensson, who supplies most of the material in the U.S., is discontinuing production of some of the Tempa material with the suggestion that it be replaced with one of the Harmony materials. This material provides more light exposure with good diffusion. It is available with open or closed weave, flame retardancy and provides a longer service life. For conservation, it can be closed during the day to provide better heat retention while still allowing good light transmittance to the plants.
In some states, the USDA Natural Resource Conservation Service has provided incentive payments to growers to replace the old existing screens. In some of the audits I have done, the payback is as low as four years.
With increasing fuel prices, the payback for conservation measures is reduced. Those measures can also improve the greenhouse environment, resulting in better plant quality.
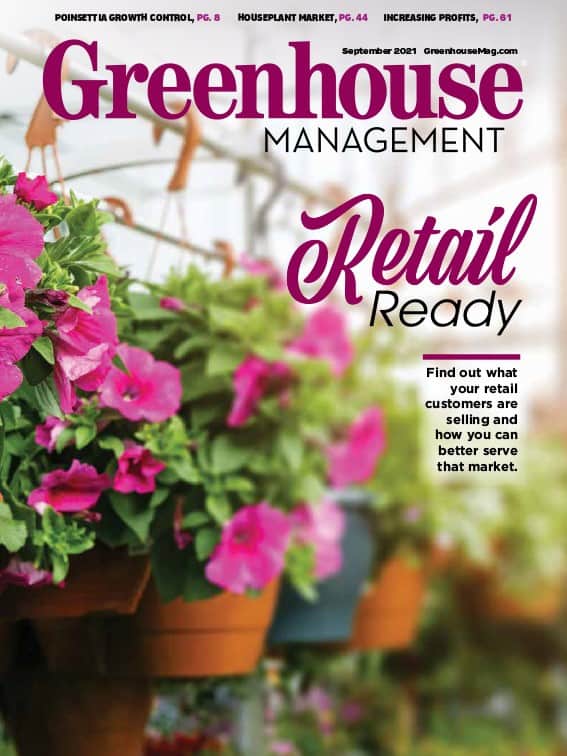
Explore the September 2021 Issue
Check out more from this issue and find your next story to read.
Latest from Greenhouse Management
- Chilli thrips (Scirtothrips dorsalis)
- GS1 US Celebrates 50-Year Barcode 'Scanniversary' and Heralds Next-Generation Barcode to Support Modern Commerce
- University of Florida offers Greenhouse Training Online program on irrigation water
- Flower trends in full bloom
- ‘Part of our story’
- Dramm introduces new hose, sprinkler attachments for home gardeners, nurseries
- Nominate an outstanding leader
- Profile Products hires sales and business development manager for Europe and Asia