
Vertical farming has been part of traditional greenhouse production for many years. Hanging basket production, roll-out trays, growing tomatoes tied to the overhead trusses, utilizing under-bench space, and starting seedlings and cuttings on carts in a growth room all utilize extra space in a greenhouse. New technology that has improved vertical farming methods include hanging basket conveyors, tray handling systems, efficient LED lighting systems and automated watering equipment.
In a greenhouse, the cost of providing the right environment is the same whether you are utilizing 50 percent of the space with a conventional bench system or if the horizontal and vertical spaces are filled with plants. Every cubic foot that contains plants means additional income dollars. The following are ways in which production space can be increased.
Hanging basket conveyor
With the development of taller greenhouses, multiple levels of hanging baskets are now possible.
Plants spaced as close as 8 inches apart are supported by a cable that moves them past work and watering stations. The convenience of having the plants brought to the end of the greenhouse for inspection and shipping can offset the cost of the system. Because plants change location, they are exposed to more uniform daily light, enhancing growth. Plants underneath the cable system will receive less light so careful plant selection is necessary.
Roll-out trays
A movable tray system can be designed to move the plants outside the greenhouse in nice weather. Employed mostly for bedding plants and perennials, it allows a grower to double the growing space during the busy spring and fall seasons. One layer of plants is grown on a heated floor and a second layer, and the roll-out layer is housed during the night above on a set of rails.
This system is common with large gutter-connected ranges where a half-acre or more of plants is pushed out through the endwall of the greenhouse in the morning and returned in the evening. It can also be adapted to individual free-standing hoophouses.

Multi-shelf carts
Carts have been used for germination and cutting production for a number of years. By adding lights under the shelves, growing time can be extended and production increased. Carts can be used in the greenhouse or in closed rooms where better environmental control can be supplied. With more efficient LED lighting fixtures now available, a more uniform light level can be achieved. Multi-shelf carts are now one of the main production system for greens in closed environments.
Stacked pots
This concept developed by Verti-Gro more than 20 years ago can increase the density of plants in the greenhouse by three to five times. The vertical stack of pots can be easily rotated to provide more uniform light. It is an easy to install system with water and nutrients supplied by gravity from the top. Harvesting of crops such as letttuce, greens, peppers, herbs and strawberries is done while standing.
High wire and trellis vegetables
Crops such as tomatoes, cucumbers and peppers that are grown from a single or double stem increase the vertical space that is used. High-wire crops that are grown supported by wires or pipe attached to the trusses or roof of the greenhouse require a structure that will support about 15 pounds per square foot. Trellis crops are usually tied to a separate frame supported on the floor. Crops are usually grown in pots, bags or troughs.
Multi-level shelves
Fixed stacked shelves are common in warehouse production of crops such as lettuce and greens. Adequate light has to be supplied to meet crop needs. A future step will be to develop systems that will move the plants as they grow making more efficient use of the light supplied. Movable stacked tray systems have been developed that rotate to give the plants sunlight and supplemental light in the greenhouse. A ferris wheel tray support system was built by a few growers in the 1970s when energy costs escalated.
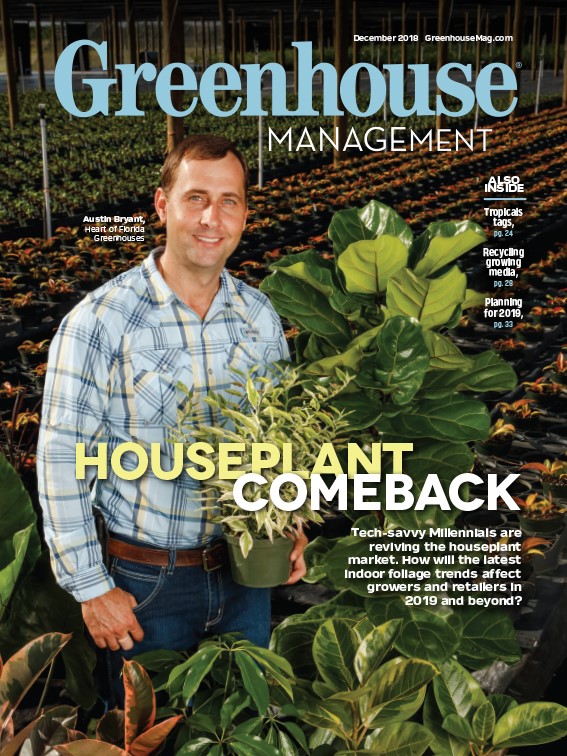
Explore the December 2018 Issue
Check out more from this issue and find your next story to read.
Latest from Greenhouse Management
- Chilli thrips (Scirtothrips dorsalis)
- GS1 US Celebrates 50-Year Barcode 'Scanniversary' and Heralds Next-Generation Barcode to Support Modern Commerce
- University of Florida offers Greenhouse Training Online program on irrigation water
- Flower trends in full bloom
- ‘Part of our story’
- Dramm introduces new hose, sprinkler attachments for home gardeners, nurseries
- Nominate an outstanding leader
- Profile Products hires sales and business development manager for Europe and Asia