![]() As a result, some growers stop using their greenhouses during the summer. But others are using specific environmental control strategies to maintain optimum production conditions. Continuous production can reduce the fixed costs per unit of plants produced and provides for a more steady labor force. Mechanical ventilation In order to maintain optimum temperatures during the summer, warm greenhouse air needs to be replaced with cooler outside air. To accomplish this, greenhouses use either mechanical or natural ventilation. Mechanical ventilation requires (louvered) inlet openings, exhaust fans and electricity to operate the fans. When designed properly, mechanical ventilation is able to provide adequate cooling under a wide variety of weather conditions throughout many locations in the United States. Typical design specifications call for a maximum mechanical ventilation air exchange capacity of 10 or 12 cubic foot per minute per square foot of floor area for greenhouses with or without a shade curtain, respectively. This air exchange capacity should be increased by 3-5 cubic foot per minute per square foot of floor area when insect screen and/or evaporative cooling pads are used. Multiple and staged fans are installed to provide different ventilation rates based on environmental conditions. Variable speed fan motors allow for more precise ventilation rate control and can reduce overall electricity consumption. Natural ventilation Natural ventilation works based on two physical phenomena: thermal buoyancy (warm air is less dense and rises) and the so-called “wind effect” (wind blowing outside a greenhouse creates small pressure differences between the windward and leeward side causing air to move across the greenhouse towards the leeward side). All that is needed for natural ventilation are (strategically located) inlet and outlet openings, vent window motors and electricity to operate the motors. In some cases, the vent window positions are changed manually, eliminating the need for motors and electricity, but increasing the amount of labor since frequent adjustments are necessary. Compared to mechanical ventilation systems, electrically operated natural ventilation systems use much less electricity and produce (some) noise only when the vent window position is changed. When using a natural ventilation system, additional cooling can be provided by a fog system. Unfortunately, natural ventilation does not work as efficiently on warm days when the outside wind velocity is low (less than 200 feet per minute). Keep in mind that whether using either a mechanical (fans only) or naturally ventilated system with no other cooling capabilities (i.e., without evaporative cooling pads or a fog system), the indoor temperature cannot be lowered below the outdoor temperature. Greenhouse design considerations Due to the long and narrow design of most freestanding greenhouses, mechanical ventilation systems usually move the air along the length of the greenhouse (the exhaust fans and inlet openings are installed in opposite end walls). Natural ventilation systems provide crosswise ventilation (using side wall and roof vents). In gutter-connected greenhouses, mechanical ventilation system inlets and outlets can be installed in the side or end walls. Natural ventilation systems usually consist of only roof vents. Ultimate natural ventilation systems include open-roof greenhouse designs, where the very large ventilation openings allow for the indoor temperature to almost never exceed the outdoor temperature. This is often not attainable with mechanically ventilated greenhouses due to the very large amounts of air that such systems would have to move through the greenhouse to accomplish the same results. When insect screens are installed over ventilation openings, the additional resistance to airflow created by the screen material has to be taken into account to ensure proper ventilation rates. Often, the screen area is made larger compared to the inlet area to allow sufficient amounts of air to enter a greenhouse. The same is true for evaporative cooling pads. Whichever ventilation system is used, uniform air distribution inside the greenhouse is important because uniform crop production is only possible when the plants experience the same environmental conditions. Horizontal airflow fans Horizontal airflow fans are frequently installed to ensure proper air mixing. The recommended fan capacity is approximately 3 cubic feet per minute per square foot of growing area. While horizontal airflow fans use a small amount of electricity, they are typically turned off once the ventilation rate exceeds some lower threshold value. Additional cooling When the regular ventilation system is unable to provide sufficient cooling for greenhouse temperature control, additional cooling is needed. Two cooling systems, the pad-and-fan and a fog system, are commonly used in greenhouses. Both make use of the cooling effect resulting from the evaporation of water. The process of evaporation requires heat that is removed from the air surrounding the evaporating water. Pad-and-fan Pad-and-fan systems can only work in combination with mechanical ventilation. An evaporative cooling pad is installed in the ventilation opening, cooling the incoming air. As the air moves through the greenhouse towards the exhaust fans, it picks up heat from the greenhouse environment. Therefore, pad-and-fan systems experience a temperature gradient between the inlet (pad) and the outlet (fan) side of the greenhouse. This temperature gradient should be minimal to provide all plants with similar temperatures. However, a gradient of 7°F-10°F is not uncommon. The required evaporative pad area depends on the pad thickness. For the typical, vertically mounted 4-inch thick pads, the required area (in square feet) can be calculated by dividing the total greenhouse ventilation fan capacity (in cubic feet per minute) by the number 250 (the recommended air velocity through the pad). For 6-inch thick pads, the fan capacity should be divided by the number 350. The recommended minimum pump capacity is 0.5 and 0.8 gallons per minute per linear foot of pad for the 4- and 6-inch thick pads, respectively. The recommended minimum sump tank capacity is 0.8 and 1 gallon per square foot of pad area for the 4- and 6-inch pads, respectively. For evaporative cooling pads, the estimated maximum water usage is 20-30 gallons per minute per 100 square feet of pad area. Approximately 10 percent of the returning water should be bled off to prevent salt buildup on the pads. Salt buildup reduces the efficiency of the pads. It is recommended that the pads dry out overnight to prevent the growth of algae. Fog systems Fog nozzles can be installed throughout the greenhouse, resulting in a more uniform cooling pattern compared to the pad-and-fan system. The recommended spacing is one nozzle for every 50-100 square feet of growing area. The water pressure used in greenhouse fog systems is very high (500 pounds per square inch and higher) in order to produce very fine droplets that evaporate before the droplets can reach plant surfaces. The water usage per nozzle is small, approximately 1-1.2 gallons per hour. The water needs to be free of impurities to prevent clogging of the small nozzle openings. Water treatment and a high-pressure pump are needed to operate a fog system. The usually small diameter supply lines should be able to withstand the high water pressure. Therefore, fog systems can be more expensive to install compared to pad-and-fan systems. Humidity control Healthy plants can transpire a lot of water, resulting in an increase in the humidity of the greenhouse air. A high relative humidity (above 80-85 percent) should be avoided because it can increase the incidence of disease and reduce plant transpiration. Sufficient venting or successively heating and venting can prevent condensation on plant surfaces and the greenhouse structure. The use of cooling systems (e.g., pad-and-fan or fog) during the warmer summer months increases the greenhouse air humidity. During periods of warm and humid outdoor conditions, humidity control inside a greenhouse can be a challenge. Greenhouses located in dry, dessert environments benefit greatly from evaporative cooling systems because large amounts of water can be evaporated into the incoming air, resulting in significant temperature drops. Since the relative humidity alone does not tell anything about the absolute water holding capacity of the air (the temperature also needs to be known to determine the amount of water the air can hold), a different measurement called the vapor pressure deficit (VPD), is sometime used to describe the absolute moisture status of the air. The vapor pressure deficit is a measure of the difference between the amount of moisture the air contains at a given moment and the amount of moisture it can hold at that temperature when the air would be saturated (i.e., when condensation starts, also known as the dew point temperature). A VPD measurement can indicate how easy it is for plants to transpire. Higher VPD values stimulate transpiration, but too high can cause wilting. Lower VPD values inhibit transpiration and can lead to condensation on leaf and greenhouse surfaces. Typical VPD measurements in greenhouses range between 0 and 1 pound per square inch (0-7 kilopascals). Shading Shade curtains help reduce the energy load on a greenhouse crop during warm and sunny conditions and they help reduce heat radiation losses at night. Energy savings of up to 30 percent have been reported, ensuring a quick payback period based on today’s fuel prices. Movable curtains can be operated automatically with a motorized system that is controlled by a light sensor and/or timer. Even low-cost greenhouses can benefit from the installation of a shade system. Curtain materials are available in many different configurations from low to high shade percentages depending on the crop requirements and the local solar radiation conditions. In some cases, multiple layers of curtains are installed that can be controlled independently for more fine-tuning. Movable shade curtains can be installed inside or outside (on top or above the glazing) the greenhouse. When shade systems are located in close proximity to heat sources (e.g., unit heaters or carbon dioxide burners), it is a good idea to install a curtain material with a low flammability. The low flammable curtain materials can stop fires from rapidly spreading throughout an entire greenhouse when all the curtains are closed. A.J. Both is associate extension specialist, Rutgers University, Department of Environmental Sciences, both@aesop.rutgers.edu. |
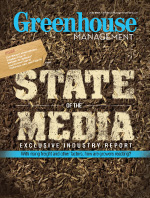
Explore the June 2011 Issue
Check out more from this issue and find your next story to read.
Latest from Greenhouse Management
- Chilli thrips (Scirtothrips dorsalis)
- GS1 US Celebrates 50-Year Barcode 'Scanniversary' and Heralds Next-Generation Barcode to Support Modern Commerce
- University of Florida offers Greenhouse Training Online program on irrigation water
- Flower trends in full bloom
- ‘Part of our story’
- Dramm introduces new hose, sprinkler attachments for home gardeners, nurseries
- Nominate an outstanding leader
- Profile Products hires sales and business development manager for Europe and Asia